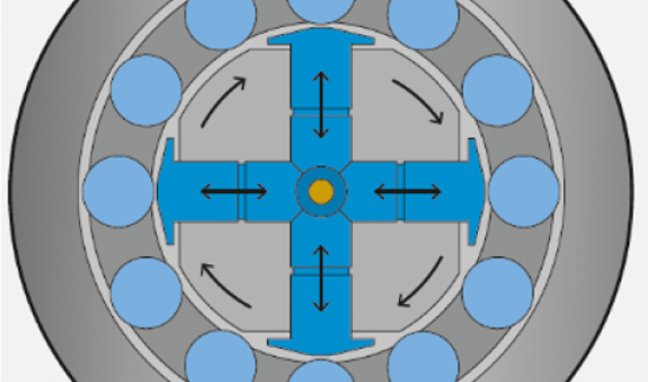
Rotary swaging
Rotary swaging is a precision process for the non-cutting forming of tubes, rods and other rotationally symmetrical workpieces.
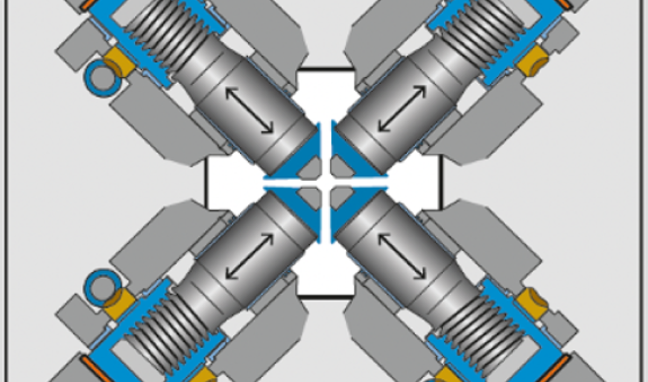
Radial forging
Radial forging is an incremental forming process for cold, semi-hot and hot forming of complex workpiece profiles.
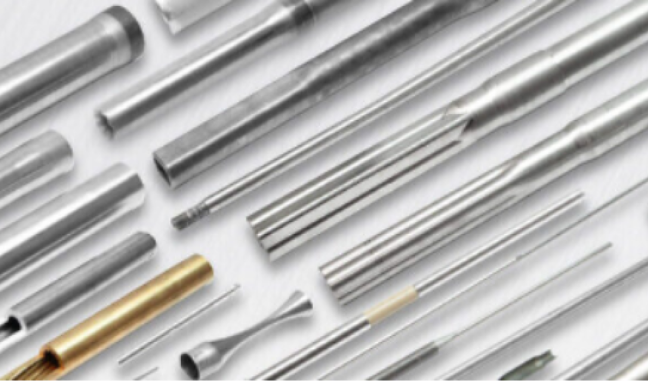
Products
High-precision production parts are custom-designed and manufactured by our experienced team for your specific purpose.
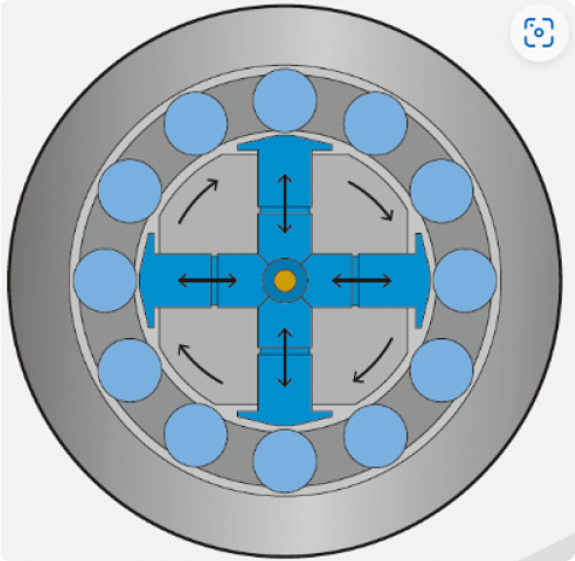
How Rotary Swaging Works
Rotary swaging is a precision process for the non-cutting forming of tubes, rods and other rotationally symmetrical workpieces.
For infeed swaging, the workpiece is moved in an axial direction continuously through the oscillating dies, while the dies rotate around the workpiece. There is a flat calibration plate in the swaging head between the hammer and die.
For plunge swaging, the dies perform a radial closing movement, in addition to oscillating radially. The closing movement is achieved using wedge-shaped hammers and calibration plates. Plunge swaging makes it possible to reduce the cross-section between the ends of the workpiece.
It is possible to combine the two variants of the process and use both infeed and plunge swaging. This involves the dies closing radially, while the workpiece is fed in axially, superimposed on top of the closing movement. This can be used to achieve undercuts of any length.
Advantages
- Short processing times
- Tight tolerances
- Smooth grain flow
- High-quality surface
- Savings on material
- Weight reduction of the workpiece
- Fewer production steps
- Environmentally friendly
How Radial Forging Works
Radial forging is an incremental forming process for cold, semi-hot and hot forming of complex workpiece profiles.
Four mechanically driven dies arranged on one plane radially form the workpiece. The workpiece is actively set into a defined rotation by the chuck head.
The hammer stroke is delivered by high-speed eccentric shafts. The adjustment unit between the eccentric shaft and the die gives you exact positioning for producing both stepped and conical workpiece profiles.
Power is transferred via an electric motor, gearbox, eccentric shafts and ram units. Particular attention has been paid to the diameter adjustment system. An advanced, patented system guarantees high-precision adjustment of the die over large ranges.
Advantages
- Cold, semi-hot and hot forming
- Combined axial and radial forming
- High forming forces
- Large die adjustment range
- No restrictions on temperature or material
- Savings on material
- Oil-free and emission-free production
- Complex inner profiles
- Very tight tolerances
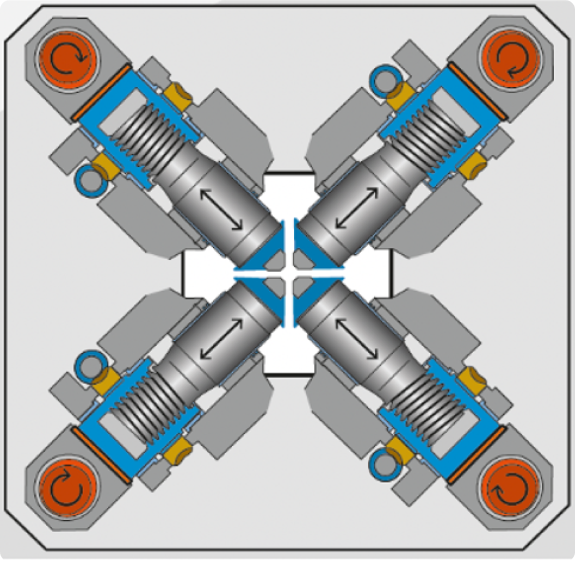
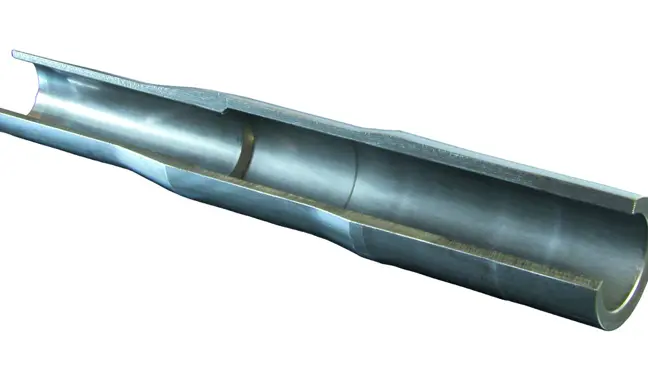
Stator shaft
- Reductions in outer diameter are produced with radial forging
- Inner profile is produced using inserted mandrel
- The interior and exterior geometry is produced in one operation
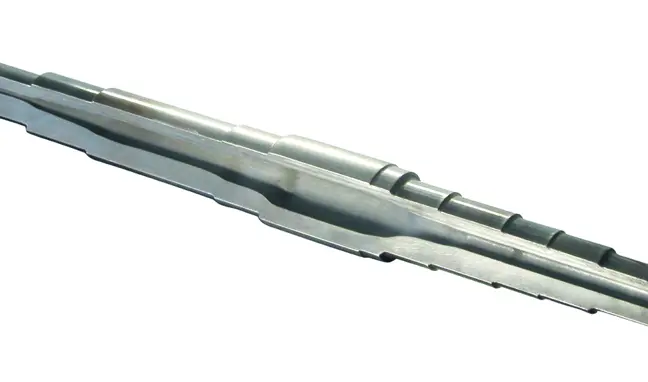
Gear shaft
-
Reductions in outer diameter are produced with radial forging
-
A section of tube is used as blank
-
The inner profile can be produced by a mandrel
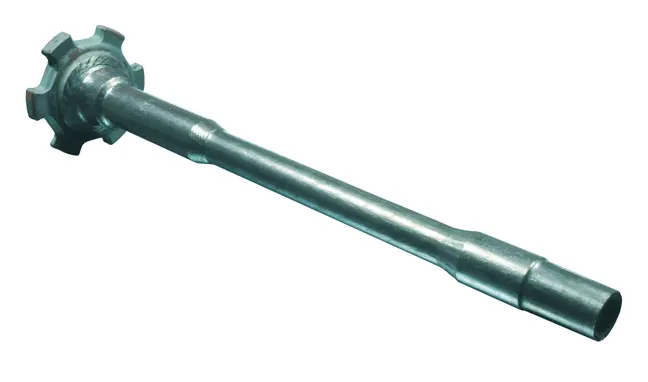
Flange shaft
- Pressed-part blank is stretched to length with different diameters in one operation by radial forging
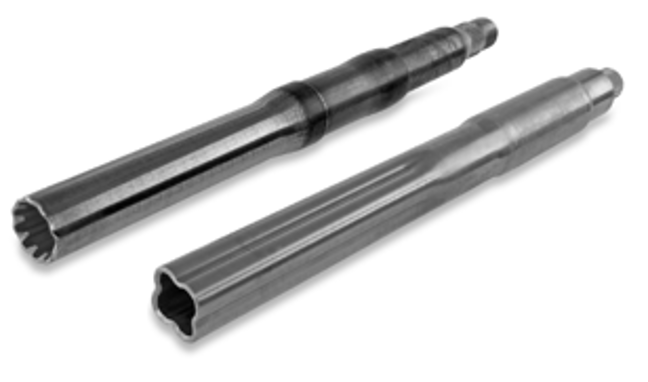
Steering column shaft
- Outer diameter reductions and profiles (cloverleaf profile and internal spline) are produced by rotary swaging
- External spline is pressed
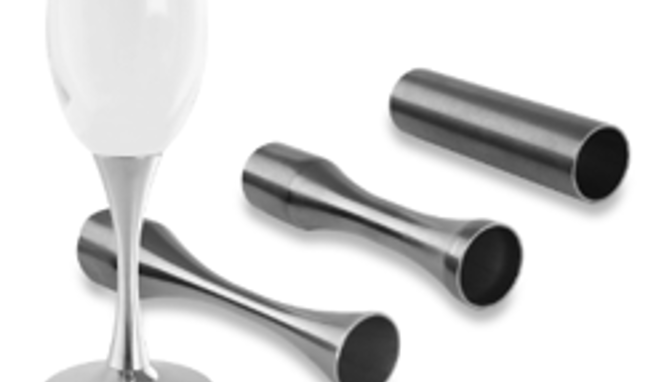
Glas steem
Rotary swaging to reduce the diameter, rotary swaging of the external hex
- Blank
- Swaging of the semi-finished part
- Rotary swaging of the finished part
- Finished part (cutting to length, polishing, assembling)
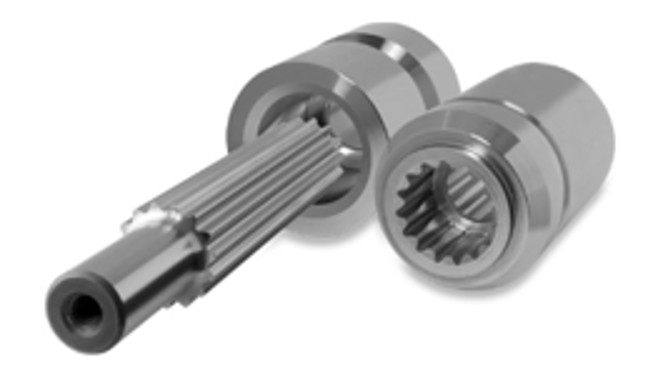
Couplung sleeve
Rotary swaging can be used to produce involute internal splines according to
- DIN 5480
- ANSI B 92.1
- ISO 4156, in a non-cutting process
The two splines can be produced in a single operation as well.
What can you expect from us?
- Whether rotary swaging, radial forging or non-cutting forming, we have all the processes in-house! We can quickly and flexibly produce your pilot series, small batch or single piece up to large batch runs at one site cost-effectively.
- With our 30 years of experience with machines from all manufacturers, we give advice that focuses on fast and precise outcomes.
- We are your industry partner for prototype production, pilot series, small series with production tools, discontinued series, parts production and process development. We are here when you own production fails too. With simple, competent and reliable service!
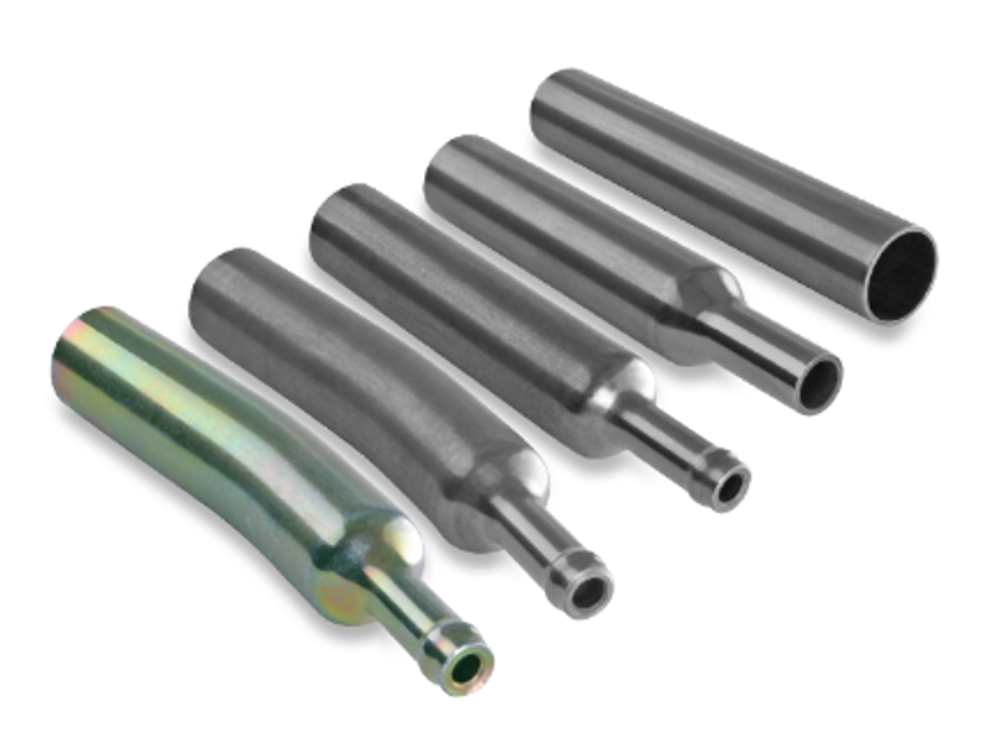
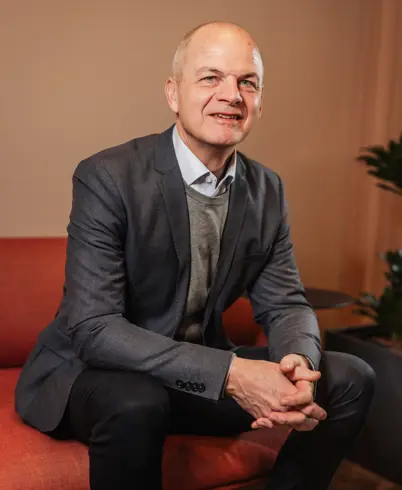